Existing Application
A food packaging company in the Manchester area asked us to evaluate potential savings from converting their old DC motor on the plastic extruding machine to a Brook Crompton World Series AC equivalent. They had previously received an energy survey that suggested a six-month payback period on the investment. Skeptical of this claim, they sought a second opinion.
DC Electric Motor Specifications:
- Power: 132 kW
- Speed: 2080 rpm
- Mounting: Foot mounted
Gearbox Specifications:
- Ratio: 63/1
- Output Running Speeds: 8 and 25 rpm
Suggested Solution
We first recommended logging power consumption over a full production cycle to gather comparative data. After analysis, the average power consumption was 85 kW, peaking at 98 kW. The motor operated for 6,000 hours annually at a cost of 9 pence per kWh. Based on the average of 85 kW, we determined that electricity costs amounted to £45,900 per year.
Additionally, the company incurred about £3,000 annually for ongoing maintenance and spare motor costs during refurbishment.
We calculated that a 1450 rpm motor through the 63/1 gearbox would achieve a running speed of 23 rpm at 50 Hz, allowing full motor power at 50 Hz (123 kW) and 30 kW of power at the 8 rpm idling speed. Therefore, we proposed a 110 kW motor.
Calculated Savings
While the DC to AC conversion calculation isn’t exact, our past experience allowed us to confidently estimate savings of 20-30%. This translates to an annual savings of £9,180 to £13,770 in electricity costs alone.
Although this payback period would exceed the six-month estimate provided by others, we based our figures on previous experience and thorough calculations.
Installation Go-Ahead
The company approved our proposal to supply a Brook Crompton World Series IE2 motor and a Danfoss FC302 variable speed controller, along with engineers for installation and commissioning.
Legislation permits the use of an IE2 motor when paired with an inverter drive. However, IE3 motors remain mandatory for all applications controlled directly on-line (DOL).
After completing the conversion, we logged the motor’s performance again to assess actual savings.
Total Savings
The savings were excellent. The average power consumed was 56kw and as a result reduced the annual running costs to £30,240. This was an electrical saving of £15,660 per year which equates to a 34% saving. Adding to the approximate £3,000 maintenance saving totals £18,660.
We offer surveys and honest experienced advice for your DC motor conversions. Contact our office for more details.

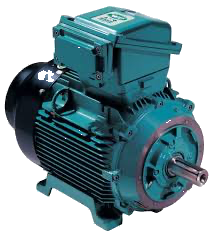